Tool Management
Control center of your production
Efficiency in industrial production is the key to success. Every work step, every machine and every tool must be precisely orchestrated to ensure smooth operation. Tool management plays a central role in this complex structure. It is the core element that keeps production processes on the pulse and ensures that everything runs smoothly.
tl;dr Efficient tool management is essential for smooth and cost-effective production. Through continuous monitoring, early alerts and quick reactions, companies can minimize downtime, avoid production bottlenecks and increase the overall efficiency of their manufacturing processes. It is the control center that ensures the smooth running of production and lays the foundation for long-term success.
The challenge of tool management
The modern manufacturing environment is characterized by diversity and dynamism. A multitude of tools, machines and processes interact with each other to manufacture high-quality products. But with this diversity comes challenges. Tools can wear out, break or suffer unexpected failures. These unforeseen events can significantly disrupt the production flow and lead to costly downtime.
Alerts in tool management
MeaningIn an ideal world, we would recognize every potential problem in advance and tackle it proactively. This is where alerts in tool management come into play. They are the sentinels that warn us of impending dangers and give us the opportunity to react quickly.
Imagine an important milling machine in your production line suffers a tool failure. Without a timely warning, this failure could go unnoticed until the machine has already stopped and production comes to a standstill. This is where alarms come in. They continuously monitor the condition of the tools and detect signs of wear or failure at an early stage. As soon as a deviation from the normal condition is detected, they send immediate notifications to the management or the relevant staff.
Importance of real-time reactions
Time is a crucial factor in modern manufacturing. Every minute of downtime means potential loss of sales and production delays. Therefore, a quick response to alarms in tool management is crucial.
By integrating real-time monitoring systems, companies can react to problems before they become critical. For example, if an alarm message is received for a tool failure, management can take immediate action to replace or repair the defective tool before a production bottleneck occurs. This fast response time minimizes downtime and ensures a continuous production flow.
Efficient resource management
In addition to preventing downtime, tool management also plays an important role in resource management. By monitoring tool wear, companies can plan in good time and allocate resources for the maintenance and replacement of tools. This enables optimal use of existing resources and minimizes operating costs at the same time.
Tool management
Our tetys solutiontetys Tool Management offers you complete management of your tools. It includes storage and tool management for toolmaking. Problems can be generated directly on the machine from the store floor via specific messages and the complete repair is recorded chronologically using our workflow. Tool management also offers you a reporting application with the option of detecting frequent errors, error-prone tools or inefficient repair processes.
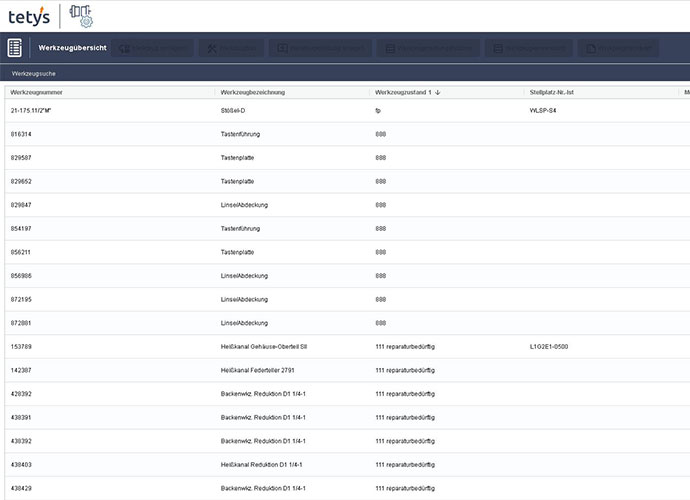
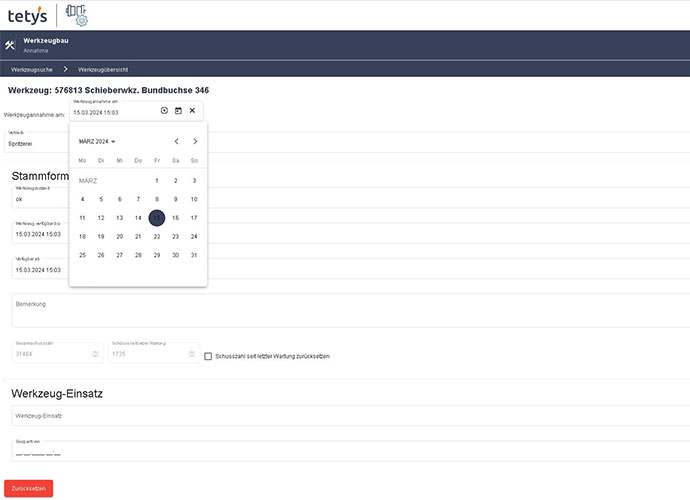
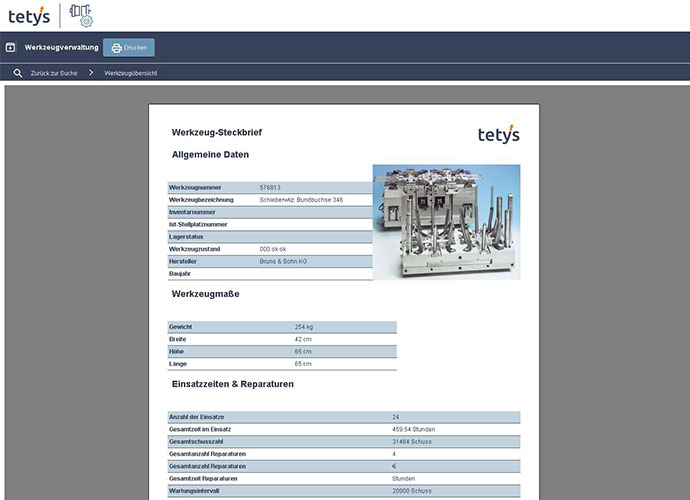
Your advantages
Traceability
Optimization
History
Conclusion
Efficient tool management is the key to successful and cost-effective production. Through continuous monitoring, early alerts and quick responses, companies can minimize downtime, avoid production bottlenecks and increase the overall efficiency of their manufacturing processes. By keeping control of their tools, they lay the foundation for sustainable and competitive production.
Are you ready to take the next step? Let's talk about what tetys can do for you.