Cost savings in production
Increased efficiency and competitiveness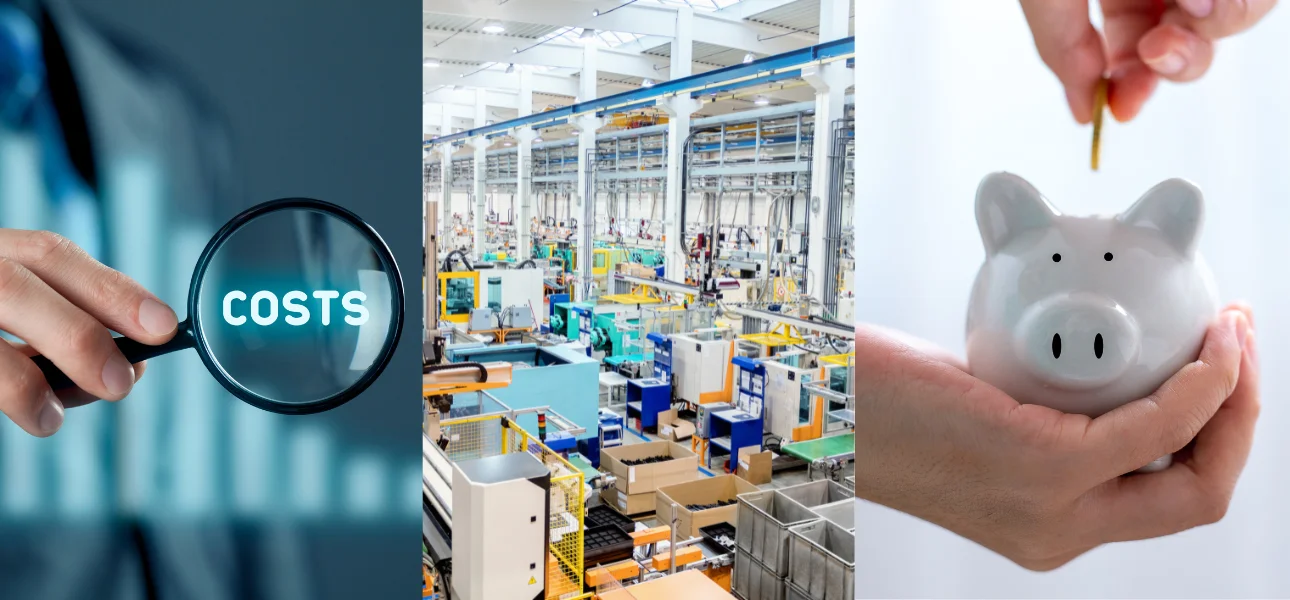
In an increasingly globalized and competitive economy, companies are constantly looking for ways to reduce their production costs while increasing quality and efficiency. The manufacturing industry in particular is being targeted, as even small savings can have a major impact on a company's profit margins and competitiveness. tetys also offers valuable solutions and approaches to improving efficiency and sustainability in manufacturing. In this article, we look at some methods for reducing costs in production that both reduce operating expenses and integrate more sustainable processes.
Automation as the key to increasing efficiency
A key factor in reducing costs in production is the automation of processes. Industrial robots and artificial intelligence (AI) are of crucial importance here. Repetitive or complex tasks are performed by industrial robots with high precision, reducing manual errors. Not only do these technologies increase productivity - they also reduce personnel costs in the long term.
Furthermore, systems based on AI make it possible to evaluate production data in real time and make well-founded decisions. This includes, for example, optimizing machine running times, predicting maintenance requirements and reducing reject rates. Companies that make data-based decisions in this way can significantly improve their efficiency and reduce costs.
Process optimization through ERP systems
Enterprise resource planning (ERP) systems are effective tools for managing and improving manufacturing processes. They make it possible to integrate production planning, materials management and logistics without interruptions. An improved production plan reduces idle times and prevents inefficient processes from generating unnecessary costs. ERP systems are also able to identify bottlenecks and reallocate resources accordingly, leading to an improvement in productivity and cost structure.
Lean Manufacturing: Minimizing waste
Another approach to reducing costs is lean manufacturing. This concept aims to eliminate waste as far as possible in all production processes. Waste can occur in various forms, such as unnecessary movements, waiting times or excessive stock levels. Companies can significantly reduce their production costs, shorten delivery times and improve overall quality by implementing lean principles.
An essential part of lean manufacturing is to avoid overproduction, as this leads to unnecessary material consumption and waste. There are various lean principles. By using computer-aided design (CAD) systems, for example, production processes can be precisely planned and simulated in advance. This leads to an optimization of the use of resources and a reduction in material waste. Another principle is the flow principle, which ensures an even and continuous production flow and thus reduces waiting times and possible interruptions.
Recycling of production waste
Recycling not only protects the environment, but is also an effective method of reducing costs. The topic is not only omnipresent in everyday life, but also in manufacturing companies. Production residues such as metal shavings or plastic waste can be collected, processed and reintroduced into the production process. This saves disposal costs and reduces material costs. Companies that consistently rely on recycling have the opportunity to significantly reduce their production costs and contribute to sustainability at the same time.
Energy efficiency with the help of innovative technologies
Energy efficiency is an area in which savings can often be made in production, but which is not sufficiently appreciated. The latest generation of machines consume up to 30% less energy than older machines. It can therefore be worthwhile in the long term to regularly update machinery.
Modern energy management systems also help to monitor and optimize energy flows. These systems identify inefficient processes and recommend actions to reduce energy consumption. Switching to energy-saving lighting, such as LEDs, is also a sensible investment. This allows companies to reduce their energy costs for lighting by up to 70 %.
Reduction of error and reject rates
Errors in production are not only unpleasant, they also cause costs. In order to reduce costs, it is therefore important to reduce reject rates. This is where quality management comes into play, for example by implementing the Six Sigma methodology. This data-based approach supports the systematic identification and elimination of error sources. The results are impressive: reduced error rates, increased product quality and lower production costs. Another method, for example, is the 5 Why method, which allows errors to be found more quickly. A systematic attempt is made to find the main cause of the error by asking the question “Why” five times. This method reduces premature attempts to find a solution or false solutions.
Material optimization to increase efficiency
The choice of suitable materials and their effective use are also crucial for reducing costs. High-performance materials with greater durability or better processing properties can improve production processes and reduce material costs. CAD systems and other lean manufacturing methods help to precisely plan the use of materials in advance and thus avoid unnecessary waste.
A comprehensive strategy for sustainable cost reduction
In order to implement cost reduction strategies in production, it is necessary to look at them from a holistic perspective. It is not enough to focus on individual measures alone. Instead, companies should continuously improve all processes in order to achieve savings in the short and long term.
Careful production planning, which takes into account all aspects such as resources, personnel and machine running times, is of great importance. A combination of automation, lean manufacturing, energy savings and material optimization provides a solid basis for reducing costs while increasing productivity and quality.
Cost reduction in production through tetys
tetys can also help to reduce costs in production, as we take care of the entire production planning. From personnel planning and seasonal planning to resource and energy savings. At tetys, we plan efficiently in order to save as many costs as possible in every area. If you are interested, please fill in the contact form in the top right-hand corner and we will get back to you as soon as possible.
Conclusion
There is a lot of potential for cost reduction in manufacturing. Whether through the use of industrial robots, the automation of processes, the optimization of material and energy consumption or the application of lean principles - every measure helps to promote the competitiveness and sustainability of a company.
Companies that continuously engage with new technologies and improvement strategies have the opportunity to reduce their expenses and thrive in a challenging market environment. The key lies in a holistic perspective and a willingness to continuously improve.
Sources
15 Ways to reduce costs in manufacturing. (o. D.). https://www.twi-global.com/technical-knowledge/faqs/ways-to-reduce-costs-in-manufacturing
Boosting industrial manufacturing capacity for the energy transition. (2024, 29. Mai). Deloitte Insights. https://www2.deloitte.com/us/en/insights/industry/manufacturing/boost-manufacturing-capacity-efficiency-key-for-energy-transition.html
Deutsche Energie-Agentur GmbH (dena). (o. D.). Deutsche Energie-Agentur GmbH (Dena). https://www.dena.de/
IFR International Federation of Robotics. (o. D.). International Federation of Robotics. IFR International Federation Of Robotics. https://www.ifr.org/
International Six Sigma InstituteTM. (o. D.). Six Sigma certifications. International Six Sigma Institute. https://www.sixsigma-institute.org/
Lean Enterprise Institute. (2024, 4. November). Lean Enterprise Institute | Learn lean thinking & Practice. https://www.lean.org/
Lean production. (2024, 6. Dezember). Lexware.de. https://www.lexware.de/wissen/unternehmerlexikon/lean-production/#beispiele-fuer-lean-methoden
Sandvik Coromant. (o. D.). Sandvik Coromant. https://www.sandvik.coromant.com/en-us/manufacturing-wellness/take-a-holistic-perspective/cost-reduction
Schörkhuber, M. (2021, 24. August). Methoden und Werkzeuge für das Qualitätsmanagement - Quality Austria. Quality Austria. https://www.qualityaustria.com/news/methoden-und-werkzeuge-fuer-das-qualitaetsmanagement/