Why there is no alternative to automated production planning in the future
Away from Excel & Co.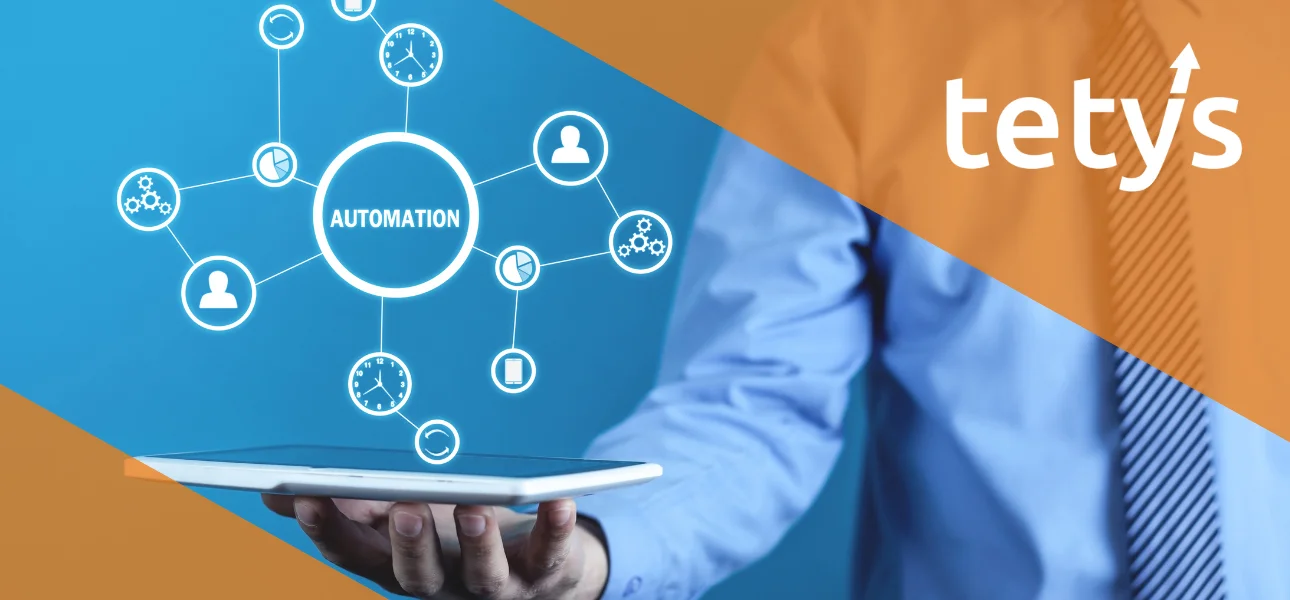
Monday morning, 6:30 am. The chaos begins.
The production manager sits with his first coffee in front of a digital mountain of Excel spreadsheets. An employee is suddenly ill, a machine is on strike and the most important customer has just brought forward an order by email on Friday evening. Now you have to reschedule everything by hand. Enjoying your coffee is out of the question.
The situation is completely different in a company that uses automated production planning. While one person is still laboriously moving cells around in Excel, the system analyzes the current situation in real time, suggests optimal solutions and even adjusts shift schedules automatically. If material is missing for production, this is also communicated directly to the purchasing department. The result is less stress, faster decisions and greater efficiency - and the coffee definitely doesn't get cold.
Why automated production planning is indispensable
Surprisingly, many production companies still rely on Excel, whiteboards or outdated systems for production planning. But if you want to remain competitive in the long term, you need a solution that keeps pace with the reality of production - preferably in real time.
If companies stick to this already inefficient and error-prone way of working, they will face another major problem: a shortage of skilled workers. Experienced production planners are hard to find, while the requirements in production continue to increase. Automated solutions take the pressure off the team and ensure stable processes, even when there are staff shortages.
In addition, customer requirements have become increasingly dynamic in recent years. Shorter delivery times, smaller batch sizes and sudden changes are now part of everyday life. Companies have to react faster and more flexibly than 10 years ago, but they often reach their limits with manual planning systems.
Another stumbling block to efficient and sustainable production planning is the limited performance of Excel. Although it is a powerful tool, it was not developed for complex production planning. Changes have to be laboriously entered by hand, and dependencies between machines, personnel and materials can hardly be mapped in real time - what's more, planning with Excel is increasingly prone to errors as complexity increases.
The solution to all these challenges lies in intelligent and (partially) automated production planning, which analyzes all relevant factors in seconds, calculates various scenarios and detects bottlenecks at an early stage.
How to make the switch - step by step
Switching from manual to automated production planning sounds complex at first, but if companies take a structured approach, it becomes manageable and plannable.
The first step is to take stock. This involves analyzing which areas of production planning still run manually and where problems regularly occur. Particularly common weak points are short-term changes, staff shortages or inefficient use of machines. Ideally, existing systems such as ERP or MES solutions should also be included in this analysis. Ideally, one or two actual processes should be optimized following this phase.
The second step involves gradual automation. It is not necessary to convert the entire system immediately. Many companies start with individual sub-areas. Automated solutions ensure optimized machine allocations and thus a significant reduction in set-up costs and prevent bottlenecks. Shift planning can also be optimized to reduce downtimes due to a lack of machine operators or setters. Modern algorithms therefore help to make the best possible use of machine capacities, taking all relevant factors into account.
Another important area is dynamic order planning. Automated systems recognize bottlenecks at an early stage and suggest alternatives to avoid delays.
A modern planning tool should also integrate seamlessly into the existing system landscape. When ERP and MES systems communicate with each other, data flows are created in real time, enabling flexible and dynamic planning.
A successful implementation depends not only on the technology, but also on the people who work with it. Automation does not mean that people become superfluous. On the contrary: planners and dispatchers are given better tools to make informed decisions. To ensure a smooth changeover, it is crucial to involve employees at an early stage and to familiarize them with the new system through targeted training and to create acceptance.
Different paths to automated production planning
Companies that want to automate their production planning have several options: Either they use their own planning software or they use a flexible service solution.
The classic solution is to introduce specialized production planning software such as FEKOR. Here, the system is individually configured and firmly integrated into the production process. The process begins with a workshop phase in which all relevant planning parameters are defined. The software is then configured and tested according to the requirements. After successful implementation, the company has a powerful tool at its disposal with which it can independently optimize its production planning.
This solution is particularly suitable for companies that want to keep their own planning in-house in the long term and have trained staff who can use the software efficiently.
An alternative to this is tetys planning flex, a service that takes over production planning as a service. Companies do not have to buy software or build up expertise in-house, but can flexibly access an external solution. Planning is carried out by experienced experts who draw on a powerful planning system and optimize processes according to individual requirements.
This solution is particularly suitable for companies that either do not have their own planning department or have difficulties with internal production planning due to a shortage of skilled workers. By outsourcing planning, companies save time and money while benefiting from professional, automated production planning.
Conclusion: If you don't automate, you lose
Manual planning was the day before yesterday. Companies that automate their production planning gain time, reduce their costs and increase their efficiency, which ultimately increases their competitiveness.
The good news is that the changeover is easier than many people think. Anyone looking for their own software solution can integrate a powerful planning system into their production with FEKOR. On the other hand, those who want to remain flexible or do not have the capacity for their own planning department can use tetys planning flex, a customized service.
Now is the right time to get to grips with the issue. Those who set the course today will secure a decisive competitive advantage in the long term.