How machine data is changing process analysis
Revolutionize your production: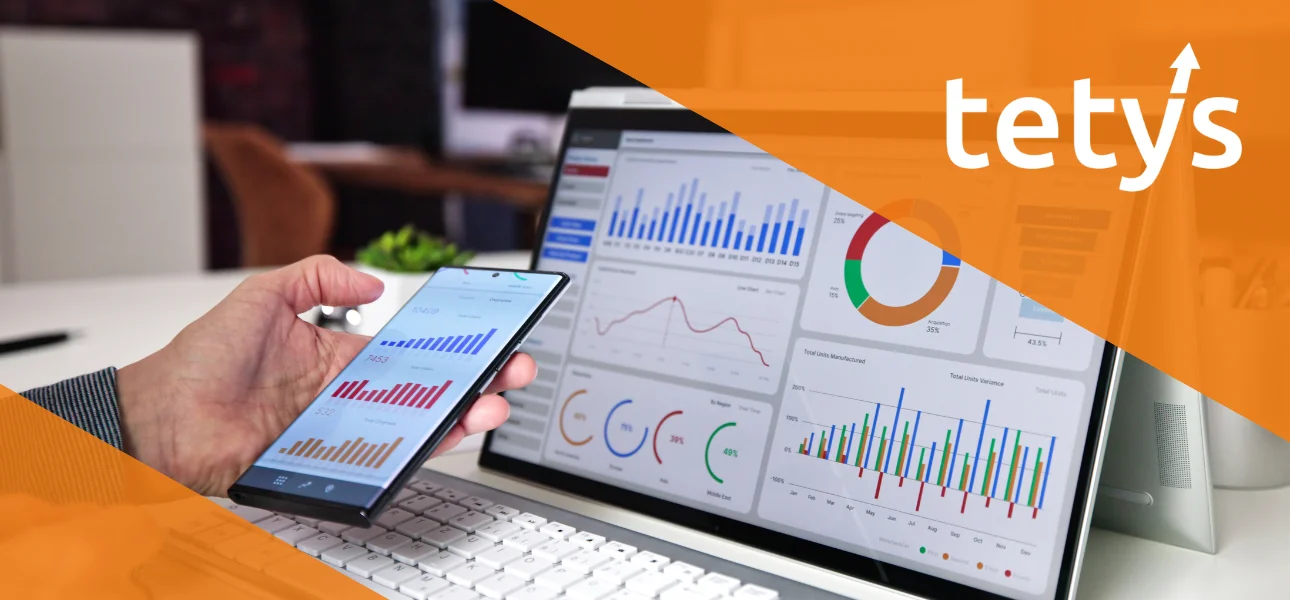
Of mountains of paper and talking machines
Imagine a production hall. Plant 3 is down, employees are standing around perplexed and annoyed, desperately searching through mountains of paper and Excel spreadsheets for the cause. Just 1 year later, the situation may be different! The machines run like an assembly line, everyone works happily and without any major problems and if a system does stop somewhere, the reason is quickly found and rectified!
And why is that? Because the company opted for our incredible software, of course! But also because the machines have learned to speak and because someone is finally listening and understanding them!
Machines “speak” with data and not words. But when you have finally found the simultaneous translator, the machines tell us where their problems lie, where bottlenecks lurk or where processes can be optimized. And we can use this to radically change production and get the best out of it!
So let's take a closer look at how machine data is changing process analysis and making production more efficient as a result!
Why machine data is key to the future
If you listen carefully to the machines, they can become a company's best advisors! Every standstill, every vibration, every rise in temperature and also quality values provide important information.
If you monitor the belt tension, for example, you can deduce from the values when it makes sense to schedule maintenance - i.e. belt re-tensioning. Such predictive maintenance solutions can also predict failures and massively reduce downtimes through clever planning. None of this is magic - it's machine data!
The biggest challenges
Now of course we are all enchanted and immediately want the data to talk to us, but in reality there are always some challenges that slow down the journey to happiness at least a little. Some of the hurdles are mentioned very frequently:
“Our machines are too old!”
Implementing new software comes at a cost, so you can't just replace the well-running systems from the 90s (or even earlier). This is usually not necessary. Using sensors or adapters, it is usually possible to create the necessary IoT-capable interfaces so that even the analog signals can be converted into digital data. So these machines can also learn to speak!
“The flood of data is overwhelming us!”
Some machines generate several gigabytes of data per day. That's far too much! We can quickly dispel this concern! The software - and we as the manufacturer - know which priorities need to be set. Nobody is left alone during such an introduction and is provided with experts. This way, patterns can be recognized and nobody gets lost in the flood of data!
“But we've always done it this way!”
Whether this sentence or the ever-popular “Everything used to be better!” - both revolve around the human factor. Because even if some people in your company are on fire to finally take the step towards the future, many employees are afraid or worried about embracing something new. We therefore always emphasize how important it is to really bring all parties to the table and listen to them.
How software turns data into real insights
So when all employees are on board, no machine is too old or produces too much data, or some other obstacle gets in the way, questions may still arise. What exactly can I do with my machine data? This is where our core competence comes into play: turning raw data into actionable overviews! At tetys, the modules are individually selected to meet the needs of each customer, but here are a few examples:
The hall diagram: the pulse of production
Tools such as our tetys MES (Manufacturing Execution System) offer the possibility of displaying the entire production in real time as a dashboard with the hall diagram module. So you can see at any time with a simple color system: Are all systems running in the optimum range? What is the status of temperatures, pressure, etc.? Is the material flow stagnating? Is an order delayed? Is a system at a standstill? What is the reason for the malfunction?
This not only gives you a live overview of everything, but also allows you to make decisions.
Predictive maintenance: repair before it breaks down
One of these decisions that can be influenced by the machine data is maintenance. Traditional maintenance works according to a schedule - often too early or too late. Predictive maintenance uses machine data to calculate individual maintenance windows. These are then scheduled into production in such a way that there is as little downtime as possible. In other words, costs and time are saved because the machine is listened to.
Quality assurance: nipping errors in the bud
You can also effectively save costs and resources by using a CAQ system (Computer-Aided Quality) or module. This links the collected machine data with a quality check. This allows deviations to be recognized immediately, and not only after a large mountain of rejects.
A look into the future
Machine data and its analysis will continue to play an increasingly important role in the future. Artificial intelligence in particular not only analyzes data, but also learns from it. This means that some things can be predicted and taken into account even earlier. We have already talked a little about the human factor and the concerns of employees. AI in particular gives some colleagues the feeling that they are being replaced by machines. In reality, however, AI makes work simpler and more efficient. Instead of spending hours looking for a fault, a message is sent in advance that a temperature rise needs to be checked on machine 3. Here, too, employees' fears should be allayed and the advantages pointed out.
In the future, networking between suppliers, external service providers and customers will also become increasingly important. In addition, evidence such as the digital product passport will come into play, which will require seamless tracking of products. Such requirements cannot be met without recording and analyzing all machine data.
Conclusion
Machine data can initiate the revolution of your finished products. If you don't just collect it in mountains of paper or cluttered Excel files. With the help of smart software and a team that is prepared to rethink, you can make the difference. It's being shouted from every rooftop that all manufacturing must now be smart and everyone needs AI. The biggest challenge, however, is to recognize what your company really needs and what you still have to deliver before software can be implemented! At tetys, we therefore first conduct workshops to assess the current situation and see which digitalization measures make sense for you. We would strongly advise you to ask yourself these questions before you rush into making your machines talk - and not spend money unnecessarily on modules or products that don't make sense for your production! You can always grow and expand, but the foundation has to be right! With these tips, you should have no more translation problems with your machines!
If you want to know how machine data can revolutionize your production, please contact us! We will show you where there is still hidden potential!
