Optimization of the production process
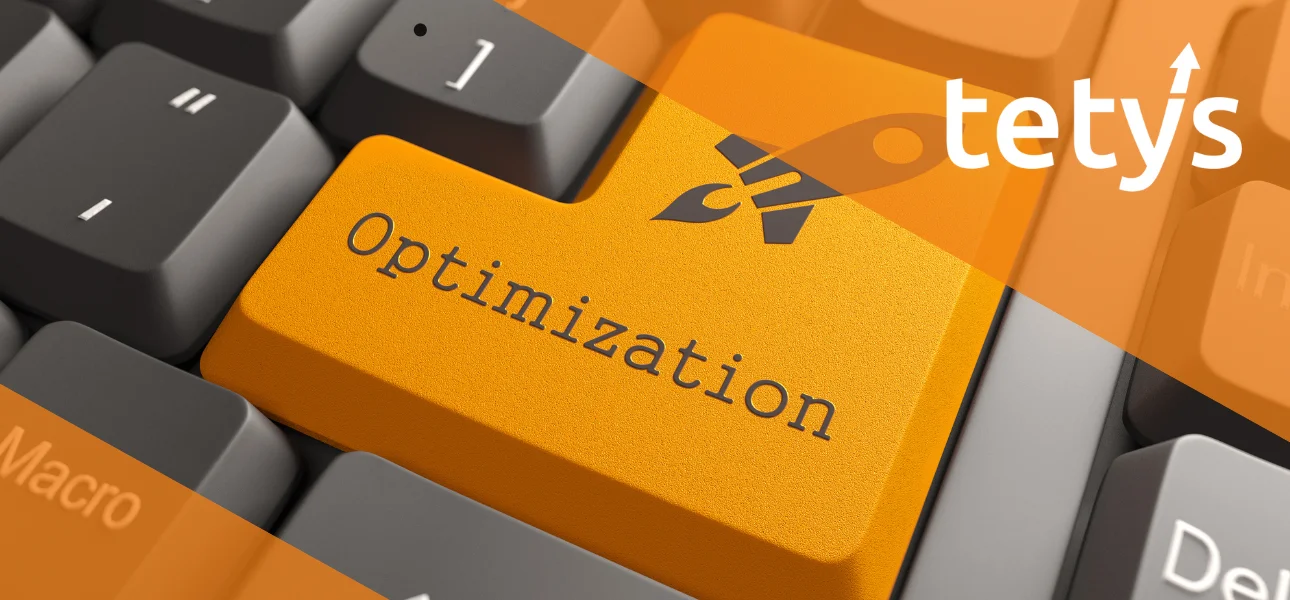
Have you ever walked through a production hall? I remember my first time very clearly. The starting point was a taster day that we had to do from school. At the time, I chose a company where a family member worked and which produced car parts. At the age of 12, I couldn't really imagine much about a production hall and had no idea what to expect. Although, I had perhaps expected to see people standing on an assembly line and handling the parts manually. Of course, that wasn't the case. When I arrived, I heard noise, saw countless machines and a few people on the move. Many machines were standing still. Even back then, I wondered why this was the case and why people were running around and why the production hall looked so chaotic. Many years later, in my current job, I was to understand how everything is interlinked. Now I know that most production processes have great potential for optimization, which has changed significantly, especially compared to the past.
But why am I telling you this at all? The topic of optimization is not only present in large industrial companies. Small and medium-sized companies also benefit from making processes more efficient, cost-saving and sustainable. It's not about changing everything overnight, but about continuous improvement and further development, which can have a big impact in the long term.
What are the problems?
We probably all know that you can only improve something if you know exactly where the problems lie. You have to understand the processes precisely and ultimately be able to make improvements in the right places. The following questions, for example, can help with this:
- Do employees often have to search for tools or materials?
- Are there a lot of waiting times because machines are not available or orders are not ready on time?
- Are there many rejected products or unnecessary material consumption?
- Where can I make general cost savings?
In order to answer these questions as well as possible, you need to analyze the production process in detail. Once this has been done and you know where there are problems in production, you can react to them and rectify the problems as quickly as possible. There are several ways to do this.
Solutions
The topic of digitalization is probably not new to any of us and can be very helpful in optimizing processes. You may now be thinking that you need to invest millions in new technologies or machines. I can reassure you. That's not the case. Digital checklists and digital documentation in general can already be a step towards optimization, as errors can be reduced and time saved. The automation of processes can also be helpful. For example, the automatic ordering of materials when stock levels are low. This again saves time and also skilled workers, as no one has to check manually. There is also the option of introducing real-time machine monitoring. This enables predictive maintenance and can prevent unplanned downtime.
The digital production passport
In today's world, however, the optimization of production processes should no longer only benefit the company and its employees, but also the environment. The topic of sustainability is and remains relevant and also plays a major role in production. This is where the digital production passport comes into play. A digital production passport is a digital document or database that contains detailed information about a product. This information can cover a wide range of aspects, including the materials used, manufacturing processes, origin, use and disposal of the product. A digital production passport provides transparency and traceability for consumers and authorities and plays an increasingly important role in the context of sustainability and, above all, the circular economy.
But topics such as digitalization and sustainability don't just start with new technologies or machines. People in companies also play a role. Regular training can help to ensure that employees know how to work more efficiently and reduce their waste, for example. Open communication is also very important to ensure that everyone is working towards the same goals and using efficient methods. Open communication goes both ways, of course, so management should also be open to suggestions for improvement and feedback, creating a two-way, positive work culture where everyone is happy. This not only makes everyone's day-to-day work easier, but also ultimately optimizes processes.
Conclusion
In summary, it can be said that optimization is not a one-off project, but an ongoing process that can be continuously developed and changed. It is important to start with small steps and first identify the actual problems. Then you can start to tackle the problems with various analyses and methods. Digitalization and sustainability play a crucial role in this and should be disregarded at the very least. Corporate culture also plays a role and the influence of employee satisfaction should not be underestimated. To put it in a nutshell: starting with small steps, the optimization of manufacturing processes can have a big impact.