Outlook for the manufacturing industry
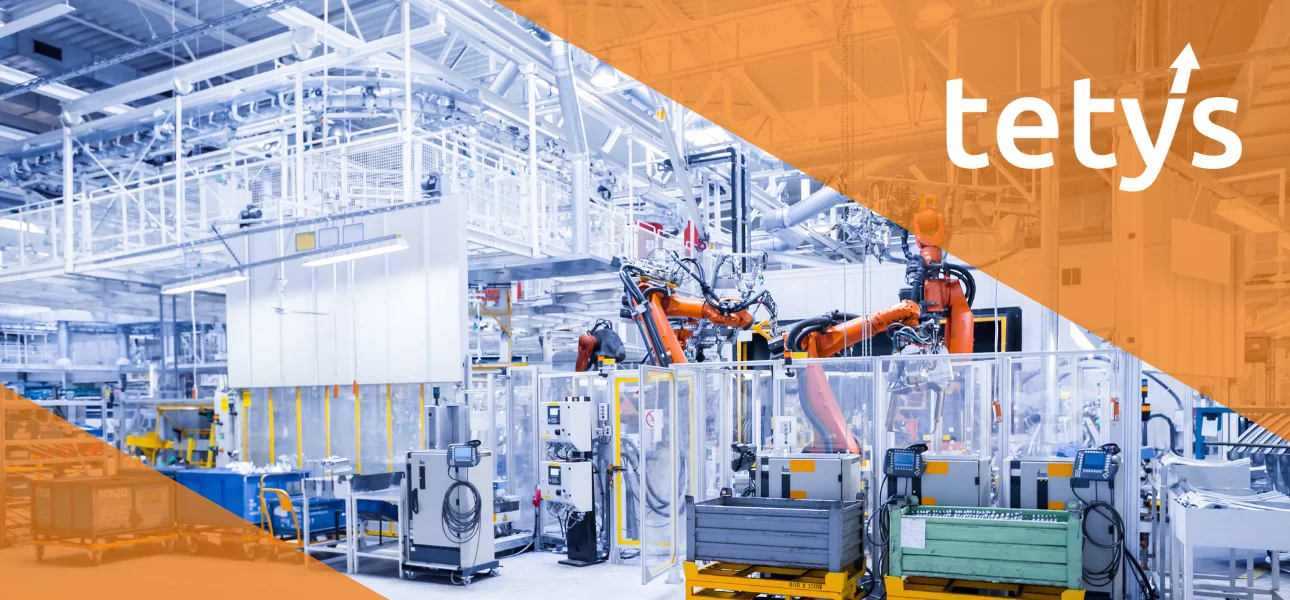
Five challenges that companies in the manufacturing industry will have to tackle in 2025
The manufacturing industry is facing a landmark year. A shortage of skilled workers, volatile markets and ever-increasing costs are forcing companies to rethink their processes. But while many are talking about digitalization and automation, a much more essential question arises for managing directors. How can my company remain competitive without risky restructuring?
Here are the five key challenges that decision-makers need to address now. Even more important, however, is the question of which solutions work in practice.
Skills shortage: automation is no longer an optional extra, but a must
Demographic change is taking full effect. Experienced production planners, dispatchers and skilled workers are hard to find and therefore even harder to retain. The pressure on existing teams is also increasing as products and production processes become more complex.
However, all the issues surrounding automation are not about replacing employees with machines. Rather, companies need to answer the question of how existing staff can be deployed in such a way that they add the most value.
One solution, for example, is the automation of production planning. Intelligent systems can coordinate orders and resources so efficiently that less operational intervention is required. At the same time, the quality of work for existing employees improves, as recurring manual tasks are reduced - increasing employee satisfaction. Companies that invest in automated planning at an early stage are less dependent on personnel bottlenecks and can position themselves more stably in the long term.
It is also worth investing in targeted further training programs. Instead of spending a long time looking for new specialists, existing staff can be supported by digital tools and trained for new tasks.
Uncertain supply chains: planning must become more resilient and adaptable
Global supply chains not only remain fragile, they are becoming increasingly unstable. Political tensions, natural disasters and raw material shortages are no longer the exception, they are increasingly becoming the rule. Those who rely exclusively on a few main suppliers are taking a high risk and run the risk of experiencing production stoppages.
The old strategy of pure cost optimization is reaching its limits. Companies need to plan more flexibly in order to adapt quickly to new circumstances. One option is to build up alternative sources of supply in a targeted manner. Those who work with several suppliers reduce the risk of bottlenecks and are less dependent on individual markets.
In addition to procurement, production planning itself can also be made more crisis-proof. Modern systems use artificial intelligence or a network of algorithms to identify potential bottlenecks at an early stage and automatically calculate alternative scenarios. Companies that invest in resilient planning can adapt more quickly to supply problems and thus secure competitive advantages.
High energy costs and sustainability pressure: ecological action is becoming a competitive factor
For a long time, sustainability was only an optional topic, but it now has a direct economic impact. Customers, investors and legislators are demanding lower-emission production processes. At the same time, energy costs are rising, making efficiency measures increasingly important.
Optimizing energy consumption in production is a decisive factor. Companies that have modern machinery and regularly scrutinize and optimize their processes can significantly reduce their energy consumption. In addition, intelligent planning allows machine running times to be better controlled so that unnecessary idle times are avoided.
There is further potential in the use of existing resources. For example, those who efficiently reuse waste heat or optimize recycling processes can not only save costs, but also operate more sustainably in the long term. In addition to direct savings, sustainable measures also bring strategic advantages. Companies with a clear sustainability strategy are more attractive to customers and can benefit from subsidy programs.
Digitalization and automation: many companies are afraid of making the wrong investment
Industry 4.0 is not a new topic. Nevertheless, many companies find it difficult to implement specific digitalization projects. There is often uncertainty about which investments really make sense and what the actual benefits will be.
The key to successful digitalization lies in a step-by-step approach. Instead of “turning the entire company upside down” at once, companies should start with specific processes that can be optimized quickly - the “low hanging fruits”. One option, for example, is to first automate individual areas such as shift planning or machine allocation for a previously defined sub-area of production.
A decisive success factor for digitalization projects is the involvement of employees. Many technologies fail not because of the technology, but because of resistance within the company. If you involve your teams in new processes at an early stage and demonstrate the concrete benefits, you can break down internal barriers and increase acceptance of digital solutions.
Volatile markets: rigid processes pose a risk
The demands placed on manufacturing companies are changing faster than ever before. Customers expect ever shorter delivery times, more customized products and maximum flexibility. At the same time, incoming orders fluctuate greatly, meaning that production capacities have to be constantly adjusted.
In such an environment, rigid processes are a major risk. Companies that stick to fixed production plans cannot adapt quickly enough to changing market conditions. In order to remain flexible, planning processes must be made more dynamic.
Intelligent planning systems make it possible to take spontaneous changes into account automatically. Instead of manually searching for solutions, modern systems can calculate in real time how changes will affect the entire production process.
Another option is to keep production capacities more flexible. Those who focus too heavily on maximum capacity utilization risk not being able to implement changes at short notice. Companies with a balanced strategy between efficiency and responsiveness are better prepared for unforeseen fluctuations.
Conclusion: the manufacturing industry must act now
The manufacturing industry is changing faster than ever before. Those who make the right strategic decisions today will secure the future of their company and remain competitive in the long term.
Companies should optimize their planning so that skilled workers are relieved as much as possible. At the same time, supply chains and production processes must become more resilient to external influences. Digitalization and automation offer enormous potential here, but the introduction of new systems must be targeted.
Sustainability is no longer just a cost factor, but a strategic competitive advantage. Companies that consistently implement energy savings and environmentally friendly processes benefit from long-term cost reductions and a better market position.
Flexibility will be crucial in the coming years. The ability to react quickly to market changes will determine a company's future viability. Companies that gear their production in this direction will secure a sustainable advantage over the competition.