Challenges for manufacturers
When production planning becomes a blind flight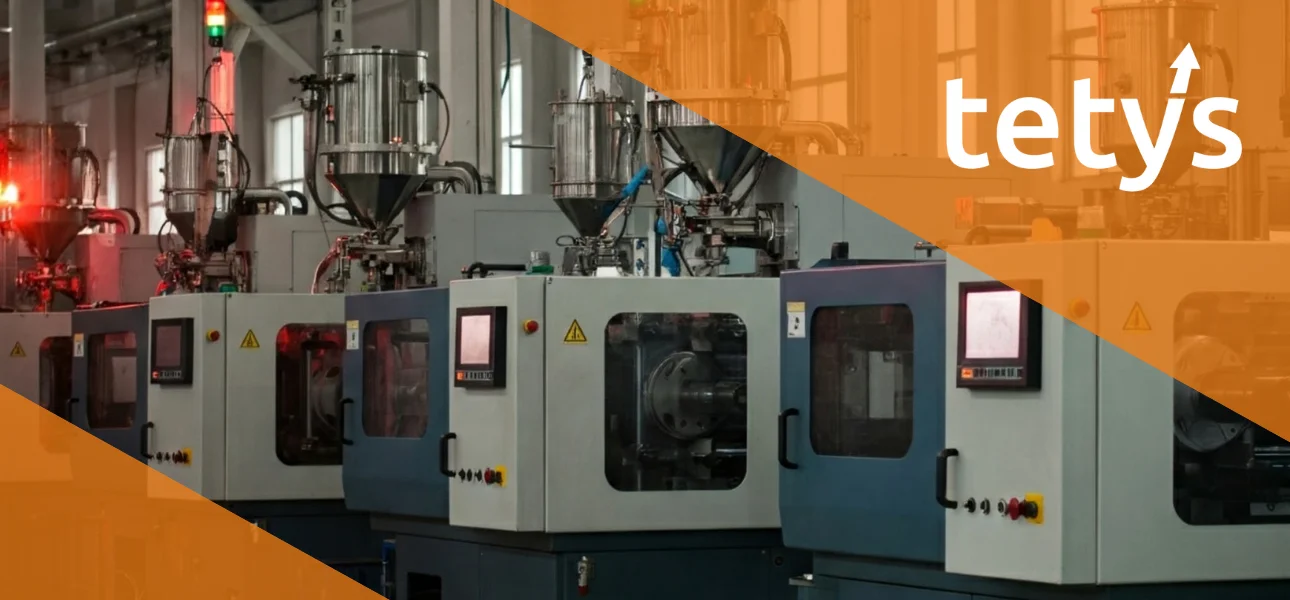
Imagine sitting in the cockpit of an airplane - without navigation, autopilot and a clear plan. You fly by sight, improvise every time the weather changes and hope for a safe landing. Sounds risky? That's exactly what happens to manufacturers who neglect their production planning or work manually - this often happens every day in industry. We are clearing up a misunderstanding here: This problem affects small companies just as much as large corporations.
Production planning is the heart of every company with its own production. It sets the pace and synchronizes everything - from the raw material to the finished product. Without a solid system or with manual methods, production planning quickly becomes a game of chance.
The challenges of manual production planning
In many manufacturing companies, production planning is still done manually. They often use Excel spreadsheets that have grown over the years or handwritten plans that are updated weekly. At first glance, this method seems practical and cost-effective. However, a closer look reveals clear weaknesses. Manual planning quickly reaches its limits, especially in modern and complex production environments. Production lines must remain flexible in order to keep up with the increasing variety of products.
At the same time, customers expect shorter delivery times and consistently high quality. In addition, there are internal challenges such as the optimal utilization of machines and personnel as well as the coordination of material flows.
Without digital support, it will be difficult to reconcile these requirements. Planning errors, incorrect prioritization or overlooked bottlenecks can have far-reaching consequences. The necessary transparency is also often lacking: Which machines are at a standstill? Where are materials missing? What is the current status of production? Manual methods rarely provide reliable answers to such questions, and certainly not at the speed required today.
The consequences of planning errors
Planning errors in production quickly show their effects on several levels. Production downtimes are a typical example. Without foresighted planning, it often happens that a machine comes to a standstill because a required part is missing or a tool is not available in time. Such downtimes are not only annoying, they also cost money.
Delays in the production chain also have serious consequences. A delayed production order disrupts the schedule and can lead to customer orders arriving too late. This affects the customer relationship and the company's reputation in the long term. Ultimately, all production depends on customers being satisfied and ordering again.
In addition to the direct consequences, there are also hidden costs due to planning errors. These include expensive rework if an order had to be completed under time pressure. This also includes the need to put in extra shifts to make up for missed deadlines. All of this puts a strain on a company's budget and reduces its competitiveness.
The influence of the shortage of skilled workers
The shortage of skilled workers is significantly exacerbating the challenges of manual production planning. In many companies, the most experienced planners are about to retire. These employees often have a deep understanding of production processes that has been built up over many years. If this group of people leaves the company, their knowledge is often lost. At the same time, it is difficult to find qualified junior staff to fill this gap. Planning requires both technical know-how and experience in dealing with specific production challenges. This includes, for example, prioritizing orders or taking machine capacities into account. This creates enormous pressure for the remaining employees. They often have to take on tasks outside their area of responsibility and have a shortage of tools. This not only leads to overwork, but also increases the error rate. As a result, the already tense planning situation becomes even more difficult.
The missed opportunities of digitalization
Many companies continue to rely on manual methods, while others are already taking advantage of the opportunities and benefits of digitalization. With digital planning tools, for example, all relevant data can be recorded and evaluated in real time. This not only enables more precise planning, but also more control over production processes.
Companies that completely forego digital solutions run the risk of being left behind. Without new planning technologies, there is often a lack of flexibility in the event of changes and possible adjustments to material availability.
In addition, manual planning can slow down a company's innovative strength, as the capacity to develop new business models is limited if there is a constant need to react to short-term problems.
Conclusion: the clock is ticking
Companies that continue to operate their production planning manually or even neglect it are putting their efficiency, competitiveness and ultimately their existence at risk, because the modern production world is too fast-moving and too complex.
But there is hope: in the next article in this series, we take a look at how modern production planning not only relieves the burden on companies, but also gives them a clear competitive advantage.